Apprenticeship Carolina Video Podcast: BMW Group Plant Spartanburg
With its $1.7 billion investment in electric vehicle production and the opening of a new state-of-the-art training center, BMW Group commits to preparing its South Carolina workforce for the next evolution of automobile manufacturing. To deliver the training necessary to transition to these new technologies, BMW Group Plant Spartanburg is partnering with Apprenticeship Carolina and the South Carolina technical college system.
Amy Firestone, VP for Apprenticeship Carolina, sits down with Paul Sinanian, manager of talent programs and training, and Eugene Grant, the operational lead of vocational programs at Plant Spartanburg to discuss the new BMW training center, the importance of apprenticeships, and how evolving technology is shaping workforce needs.
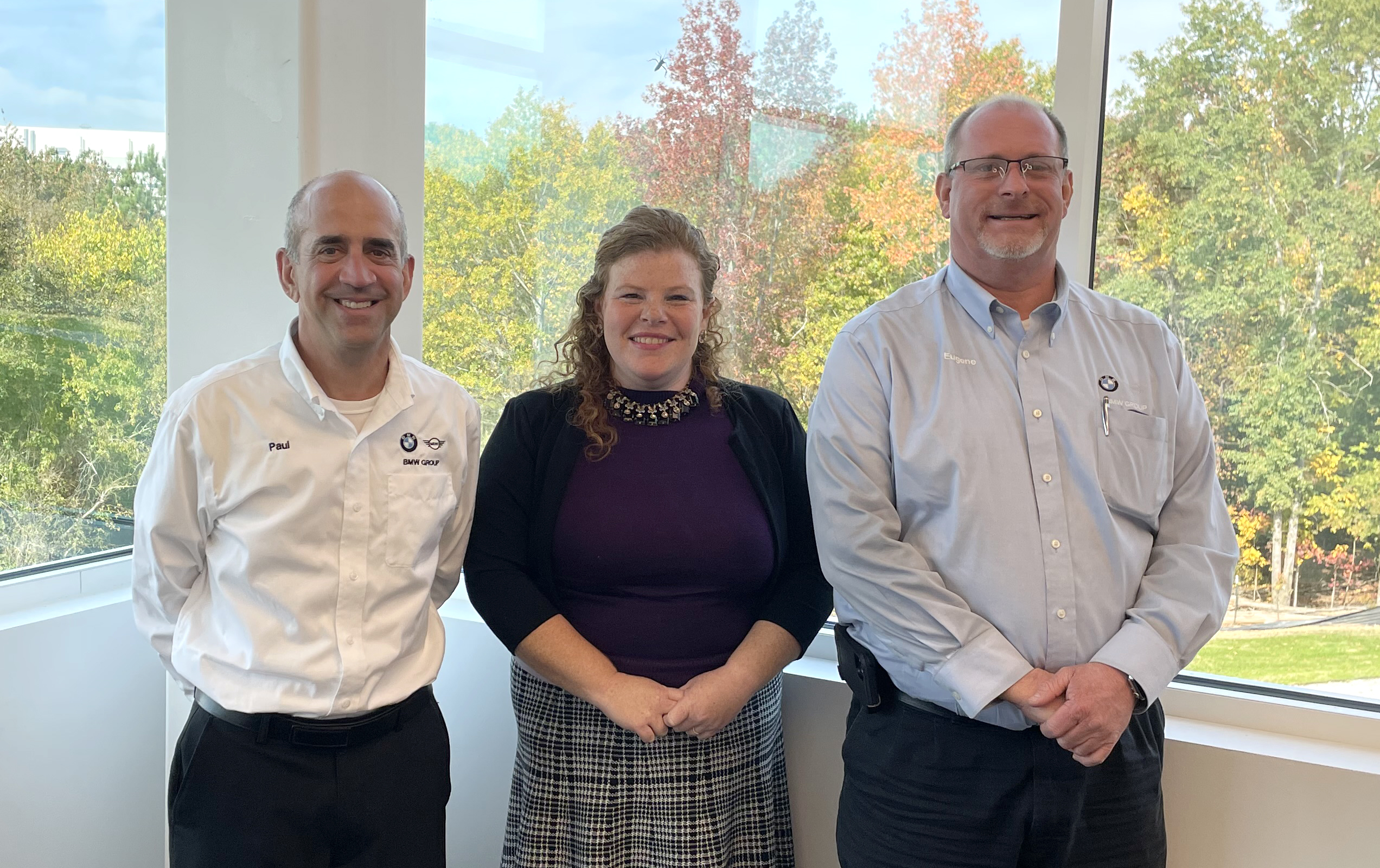
Amy Firestone: Hello, everybody. Welcome to Apprenticeship Carolina's second podcast. We are here reporting from Plant Spartanburg at the BMW plant and their new training center. It's a very exciting day because we are in November, and it is South Carolina apprenticeship month. We are here to really get to know a little bit more about BMW's work as a trailblazer with apprenticeships in South Carolina, how they're supporting youth and adults through training them through very innovative technologies. And we're here to learn a little bit more about two of the leaders at BMW and how they are making this program happen.
About Apprenticeship Carolina
Before I jump in and introduce our BMW leaders for today, I wanted to tell you a little bit about Apprenticeship Carolina if you're new to us. Apprenticeship Carolina is part of the South Carolina Technical College System, and we help support businesses from all industries to develop and implement registered apprenticeships with the US Department of Labor. We've been doing this since 2007. We work with over a thousand businesses statewide helping them advance, helping them cultivate the next level of talent both working with youth and adults across the state.
So today we're here to learn more about apprenticeships and training at BMW, and really look at the registered apprenticeship model which is what Apprenticeship Carolina has helped so many businesses with since 2007.
You might ask, ‘what are registered apprenticeships?’ And we can start there because to learn more about BMW's model it's good to have some basic foundation. Registered apprenticeships have been available in the US for over 80 years, and they are programs that are called ‘earn while you learn’ programs. They combine on-the-job training with classroom instruction, and that classroom instruction can happen at one of the 16 technical colleges in South Carolina, at a career and technology center at a high school, or a combination of many different educational centers. They provide mentorship to youth and adults who are learning a brand-new career pathway.
Introduction to Paul Sinanian and Eugene Grant
So, BMW has been advancing in this space for a while in South Carolina and I have two very special guests with us here today. I would like to introduce them: Paul Sinanian, who is the manager of talent programs and training at BMW. Welcome, Paul, thank you very much for this opportunity. And we have Eugene Grant, who's the operational lead of vocational programs.
Those are two pretty big charges here at BMW and as you can see, we are right now in the beautiful new training facility with behind us the Plant Spartanburg. What a gorgeous view and thank you for being here. I want to start out and ask both of you if you could just tell us a little bit about your roles at BMW and what you do to support training, and Paul, we'll start off with you.
“Workforce development is crucial to our survival and the workforce is changing and the technology that we're dealing with is also changing, so we've got both the challenge of bringing in new talent but also to continue to develop the internal talent. That's a constant cycle and we know that something else will change a few years from now. So we're not building a team of associates and team members to just get us through the next few years, we're building that workforce to be able to get us through the next 30 years.”
— Paul Sinanian, manager of talent programs and training at Plant Spartanburg
Paul Sinanian: I thank you Amy, thanks for having me. I tell people I have the coolest job at the plant I get to deal with new young talent. I get to deal with continuing to develop all the associates that we have in the company and working with new technology and I've been fortunate enough to be a part of the new project to build this new training facility, for the opportunity to really bring a new level of tools, to be able to upskill our workforce. So I'm responsible for all of our talent programs, all of our programs for apprenticeships, all of our programs for college internships, all of our talent development programs, and on the flip side as well continuing the training and leadership and professional development training here at BMW.
Amy: Fantastic, Paul. And how did you get into this type of work at BMW? What led you here?
Paul: As an engineer, it was kind of something that was new for me. I was asked to come over and work on the training center and then I happened to be at the right place at the right time and they asked me to take over the training group, and it's been a fun journey. I've been in this role just three years and I've been at BMW now 25 years. I was in the product validation group, so I have worked from the car now to our most valuable asset we have in the plant, and that's our associates.
Amy: Wow, I'm sure you've seen a lot in those 25 years, especially with all the new innovations and equipment and just the different projects that you've talked a little bit about. So we'll hear more from you in a few minutes, but Eugene, tell us a little bit more about what you do here at BMW and how you support training in the apprenticeship programs.
Eugene Grant: I'm responsible for the vocational talent programs within the plant, which are external and internal. With our registered apprenticeship programs, which we call Scholars, we're working externally where we're bringing in young talent or even non-traditional students where we're looking at some older adults who are maybe looking at a career change and wanting to come in and do something different as well as some internal programs where it creates some promotional opportunities and growth for our internal associates. I have the luxury of having one goal and that's to make learning fun and so we try to do some really cool and innovative things because I think you learn by doing. And we try to hit the different learning styles that a lot of people have and so the main portion of it being experiential learning. I think that's the key.
Amy: And if you could tell me what inspired you to get into this type of learning and to carry on that learning, that message to all of the future and current employees here at BMW.
Eugene: It was a total accident. For me it started back years ago. I was in maintenance and one of my professors at the time asked would I be interested in teaching a lab for him. So I taught that lab, a digital circuits lab, and I will never forget it. When I left that evening, I knew what I was going to do for the rest of my career. And ever since then I've been in some form of education or a learning environment developing the workforce.
Amy: That’s fantastic. so really a mentor, professor really inspired you, and you're doing that now with all of the young people and adults in the community here.
Eugene: Yeah, for about 32 years now, I've been involved with adult education, either at the company level or with the technical college system. I think that's been one of the biggest advantages for me, is being a byproduct of our technical college system itself. It shows the growth that can occur. You don't have to necessarily come from a traditional four-year university to end up in very successful career fields.
BMW’s Training and Apprenticeship Programs
Amy: Exactly. We want to hear a little bit more about that and how BMW is helping provide multiple career pathways through apprenticeships and obviously other training programs that you have. So could you tell us a little bit about what BMW offers right now in terms of the apprenticeship programs or apprenticeship type programs that you all have -- new ones and ones that have been in existence. Tell us a little bit about those programs.
Eugene: We started our first registered program here in 2011. In fact, we're getting ready in apprenticeship month we want to recognize our 10-year anniversary of our first graduating group and we call that our Classic Scholars Program. And within that particular group we have typically three traditional professions. We have a mechatronics, automotive and logistics/supply chain but the one thing that we noticed over the last few years especially since Paul's come on board our group, providing some strategic leadership with it, is we were missing some pools of people. And one of those pools was at the high school level and so we took a really hard look at what we could do to open up a new program a youth apprentice program.
So we started that up two years ago now and we call it our Rising Scholars Program so we work with our local CATE centers and focus on automotive and mechatronics with them and so we're bringing in young talent there, which is really great because I think the younger we can capture that talent the more that we can groom them and shape them into the employees of the future that we want them to be.
And then our other brand-new program that we've just started is what we call our Fast Track and this was designed for students who went to the technical college and have graduated but didn't have any work experience so they couldn't apply for any of our local jobs here. And so we knew we had a hole in the system and so we said, ‘well why don't we bring them in and just put them through a one-year fast-track program to fill in the gaps and so that's what we've done. And so now between the three programs we're able to capture three different pools of people in stages within their educational career path, and I think that's been very successful so far. That's just one of our pillars of our training group. And I’ll throw it to Paul to talk a little bit more about our workforce development programs.
Paul: What we talked about is a talent pipeline, and what you heard from Eugene is this is our approach to bringing that new stream in. What we want to make sure is that we turn over every rock, look at every area of the workforce and say, ‘okay, what else could we do to be innovative and look at the non-traditional streams of talent.’ We all know the challenges that we're having in the industry right now in the United States of workforce development and really filling in some of these key technological areas.
So we had to get creative and we looked at everything and said, ‘okay, how do we get more creative but make sure that we continue to build that workforce that we need with all the new technology coming and also not ignoring that we have a talented workforce already here that we may have to upskill for new technologies that you can continue to develop. So fortunately for our group, we have the entire array of activities from talent pipeline through all development of professional development and technical development so we can continue to build the entire workforce, both the incoming and the current workforce to that level that we need for all this new technology.
Amy: It's very impressive. Lots of opportunities, no matter what age you are. Obviously 16 as a minimum age or 17 here at BMW and just different levels. Can you tell us a little bit about how many people are already participating in these three different programs? That's the first part. Second part is if you're watching here and you're a parent or maybe you're in high school or you're in college, what does it take to join them? What do you need to have and what is BMW looking for to enter these apprenticeships?
Eugene: With our Rising Scholars we're bringing in 24 – it’s the number that we're currently targeting. With our Classics program, we're bringing in 70 total, and then with our Fast Track we're bringing in 16 between now and December. It's spread across the spectrum of the different professions that I mentioned including us bringing in a few IT as well as machine tool for tool and die work with our new stamping plant. Those were the three growth numbers that we're trying to target.
And I apologize, what was your second question?
Amy: If you have a parent out there, or maybe someone in high school or someone who just graduated from a technical college and they want to learn all about these programs, how can they get more information and what are the requirements?
Eugene: Actually, the easiest way is to go to Google and Google ‘BMW Scholars Program’ and the first link that pops up will send you to our webpage. The webpage is www.bmwusfactory.com and from there, you'll click on the link to apprenticeships, and that's the easiest way to find out more descriptions about our three programs and how to go about applying. You can also reach out to any of our four partner colleges, which is Spartanburg Community College, Tri-County Technical College, Greenville Technical College and Piedmont Technical College, and they can point you to the website as well and walk you through the steps that's needed to apply.
Amy: We’ll put your cell phone number on the screen, Eugene. (Laughs) No, we won’t do that.
Eugene: Yeah, I'll save that for Paul.
Paul: Amy, those are the technical requirements of what it would take to get in here. What I would say is this as well. So let's look at the more transformational assets of what we're looking for. We're looking for problem solvers and at the end of the day we're looking for people who want to have a career BMW, not just to come in and do a job, but to have the opportunity to come in to learn a role, to learn a skill set that they can build the foundation for a career. We want somebody to come in and join our family and work with our culture and never want to leave. I want somebody to come in and build the skill sets because we have lots of opportunities here. We're an international company, we've got so many different technologies operating under one roof that we want to give the opportunity to really build a skill set and to feel like they're part of an organization that cares about them and wants to advance their career. And I tell them at our orientation, I want to be here for your retirement.
Amy: Fantastic. And maybe this is for you, Eugene -- working with so many different young people who are figuring out what their pathway looks like at BMW, what would you tell them is the most exciting thing about working here as an apprentice, or somebody a little bit further in their career?
Eugene: I think to me it’s the product. The product sells itself. I mean it's a proud place to work because you have the opportunity to see the products that were produced and the satisfaction that you see on customers’ faces through videos and stuff. But then it's back to what Paul was talking about, the culture and the environment, to me that's the key. Because Paul mentioned too, our most important resources are people. And so I think bringing in the right people, with the right mindset and the right attitude, that's the key to creating an environment where people are going to thrive whether they come in one specific role and then want to move over to another. A prime example is some of the growth that we've seen in our Scholars Program. We now have people who have finished the program that are higher than me within the organization, so you can see the talent as it grows.
But back to Paul's point, you don't want people to leave. You want to create that environment where they don't want to leave us and so I think that's the key is that you create that innovative, risk-taking excitement that you try to continually improve and get better, and I think that kind of culture is contagious and so that's the secret.
Amy: And how would you all say that apprenticeships are helping you with that goal?
Paul: It's interesting because, again, I started on the product side, so I got the opportunity to really experience the excitement of the product. And now I'm just as excited if not more about seeing young talent come in and build the foundation of their career and you can see that excitement that builds when they have the confidence, they have the tool set. They start to explore a little bit, and they're not always succeeding. They're being challenged, so this role is not one where you're going to come in and succeed right off the bat. You're going to learn, you're going to build a tool set, a set of tools that you can use throughout life. You can use it throughout your career, but you also can build that leadership. You can build that sense of team. You can build that sense of culture as well.
Investment in EV and South Carolina
Amy: I really love to hear all of this because I know that you're continuing to grow and there's been a lot of announcements from BMW lately and I'm sure our viewers have heard a lot of exciting things. Just on October 7th, this beautiful training facility was launched and then there are some other announcements. There's this number floating out there: 1.7 billion. Paul, Eugene, can you help tell us what that number is and what that's going to do for you for the training center and for all the great things happening at BMW for current apprentices and future apprentices?
“The 1.7 billion dollars is an investment in this plant, it's an investment in this workforce, it's an investment in this state. We're home here and we're going to make sure that our home is prepared for the future.”
— Paul Sinanian, manager of talent programs and training at Plant Spartanburg
Paul: Well, that's easy. You're looking at an investment in this plant and investment in the people of South Carolina and it's a continued view of the cooperation and the collaborative relationship we have with the state of South Carolina. What we're doing with that 1.7 billion dollars is building the opportunity to prepare the current plant for the electrification that's coming with our new vehicles, so the infrastructure, the talent development, everything that we need here, and we're also building a new plant to fabricate batteries to be able to support the new battery vehicles that we're going to be building here. So the 1.7 billion dollars is an investment in this plant, it's an investment in this workforce, it's an investment in this state. We're home here and we're going to make sure that our home is prepared for the future.
Amy: Fantastic. And Eugene, since you're working a lot with the students yourself, can you tell us what does that mean for you and your role and how you're going to work with the current apprentices and all the future ones that will come here?
Eugene: To me, that's the exciting thing about being in the role that I’m currently in. The technology is constantly growing and changing and that's the same with our battery technology. And so those are the exciting things for us, to take that new technology and then make it accessible for the new young people coming in and so they can see the history from the older technologies and up to current. The key is I have a fundamental strong foundation on which to then build these newer technologies that are coming in. It's like Legos, you just keep stacking it on and I think that's the key and from that it just builds up to whatever your career goals may be. For me, it's the new technology, it's excitement, and that excitement then bleeds down to them because they want to be learning the cutting-edge things that are out there.
Amy: EV and Legos that kind of sounds intriguing, but I won't take us in that direction (laughing.)
Will current apprentices get to work with this great goal that BMW has that half of your sales will be for EVs by 2030? Is that something that the apprentices will get to help work on and learn about?
Paul: Absolutely. That's the thing we have to understand. Workforce development is crucial to our survival and the workforce is changing and the technology that we're dealing with is also changing, so we've got both the challenge of bringing in new talent but also to continue to develop the internal talent. That's a constant cycle and we know that something else will change a few years from now. So we're not building a team of associates and team members to just get us through the next few years, we're building that workforce to be able to get us through the next 30 years. It's a continual challenge to make sure that we're always up to date but the investment in this training center is one that we knew was going to be necessary to be able to do that at the right level for the future.
Amy: Eugene, anything you'd like to add to that?
Eugene: You've got to take what is in the pool of candidates that's out there and then take and grow them into what you need them to be. Back to Paul's point, we're not looking today and tomorrow, we're looking three and five and seven years down the road. So what we're trying to instill in them is really the things we want to see that's going to help us be there in seven years and in ten years.
Benefits of Apprenticeship
Amy: Exactly. There's just so many exciting things happening here at the plant. And for people who aren't even in high school yet, just something to think about as you think about your future career. But I do have another question for you all to kind of wrap up. As a business, what would you tell other companies in South Carolina, whether they are German companies, European companies, or American companies, about the apprenticeship program and how it benefits BMW? Obviously, we know how it's helping with your workforce needs, but what would you tell them as kind of a closing point and why they should look at what you're all doing as the apprenticeship model?
“To me this is the easiest way to attract, retain and develop people for the future of your manufacturing area.”
— Eugene Grant, operational lead of vocational programs at Plant Spartanburg
Eugene: For me, I think it's a great opportunity that the state has provided all of us manufacturing companies to work with Apprenticeship Carolina, to seek their expertise on how to set up these training programs and to help us grow our future workforce. As the state attracts more and more manufacturing companies, we're all struggling and fighting for the same talented people that are out there, so you have to be able to grow your own in a lot of cases. To me this is the easiest way to attract, retain and develop people for the future of your manufacturing area.
Paul: To me it's really simple. It's paradigm shift. As the industries that you support, we've got to be able to think in a different way. It's no longer ‘why we can't,’ it's ‘why can't we? Why can't we do this? Why can't we try this? And what companies need to do right now is to think ‘why can't we do that?’ And that's exactly where we went with our Rising Scholars Program. I went on a business trip, and I saw it somewhere else and I walked back to these guys and I said, ‘why can't we do that?’ That's what ignited this movement into turning over every stone and trying everything possible.
What I think has to happen is companies need to sit back and say we've got to be more creative and more clever on how we do this. And you guys have been a fantastic resource to us because we bounce ideas off you all the time, and some of the things work but some of the things don't. But at the end of the day, if you don't ask the questions, you don't get an answer yes or no. So I would say this, why can't we?
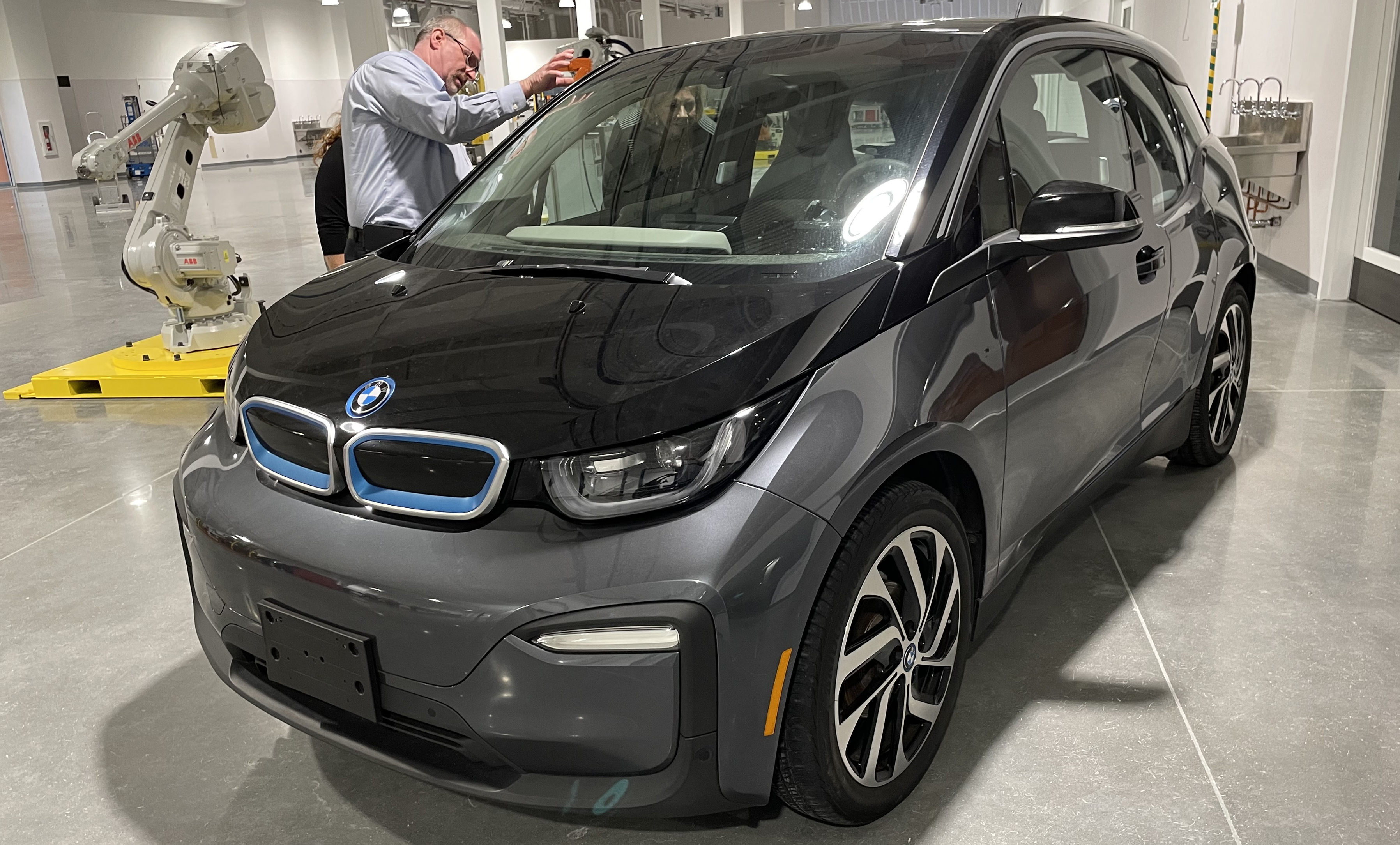
Electric vehicles are incorporated into the BMW training center’s learning environment.
Amy: Really good point. As our viewers know, Apprenticeship Carolina’s service is provided free of cost to any business in South Carolina. We help you design the apprenticeship, help you revise the current apprenticeship, help you with grant funding. We have up to three thousand dollars right now for tuition, books and supplies and up to a thousand dollars for stipends. So just reach out to us if you're interested in those resources. And obviously meeting with companies such as BMW to help them assess their current workforce needs and new apprenticeships that we can create either at the youth level or at the adult level, that's something that we do every single day.
Looking to the Future
Amy: I know you all can't share any other big announcements with me here because that's not how things work, but is there anything exciting you want to leave with our audience just to wrap us up in terms of something new that they can look out for?
Eugene: I think for me, some things that we're looking at: working with our educational partners at the elementary, middle school level. You may see some exciting things coming there in the near future.
Paul: That was going to be mine, so he stole my answer (laughing.) We've got a mature strategy now for dealing with universities, for technical colleges, for community colleges and now into high schools. And I came back to them and said, ‘why can't we go into middle schools? Why can't we go into elementary schools? Why can't we go to special interest groups?’ We just had a conversation yesterday to say ‘why can't we cover more of the South Carolina team members and potential team members we see out there. So we're turning over every rock to try to find even more people that we want to be able to bring into our team.
Amy: That is really exciting! So all of the elementary school children out there and their parents and family and relatives can maybe see Eugene and Paul coming out there – maybe not you all, but some of your colleagues – and that's really exciting to help spread the word about the great opportunities that BMW can provide. Not just for the short term, but for that long-term career that Paul was saying would like to see you at your retirement party whenever that happened.
I want to thank you, Paul and Eugene, for taking time out for us. I know how busy you are with this brand new center that you've opened and all the new projects ahead. We're just excited that you're celebrating 10 years of the tech scholar program. That shows a tremendous success that you've had and all the new employees who have gone through that program and what they've gained and how they're helping be part of this new chapter for BMW. We are just very happy to be working so closely with you all on these expansion efforts. We want to thank you for your time again, (turning to camera) and thank you all for joining us.
Eugene: Thank you.
Paul: Thank you, Amy. And thanks again for all of the support that you guys have given to us. It’s really been a game changer. We appreciate it.